یکی از پرهزینه ترین و مهم ترین مراحل در فرآیند فرآوری مواد معدنی آسیا کردن می باشد .هدف از آسیا کردن بدست آوردن درجه ی آزادی مناسب از کانی با ارزش می باشد .آسیا کردن به دو طریقه خشک و تر صورت می گیرد.نوع کانی با ارزش تاثیر مستقیم درانتخاب طریقه ی آسیا کردن دارد . دومین عامل موثر در انتخاب طریقه ی آسیا کردن مراحل بعد از آسیا می باشد .که آن هم به نوبه ی خود می تواند محدود کننده باشد .آسیا کردن در کانه های فلزی و غیر فلزی متفاوت می باشد.
آسیا های گردان به صورت افقی فعالیت خود را انجام می هند. و در جهت افقی حرک می کند .هرچقدر ذرات ماده ی معدنی ریز ترباشند عمل نرم کردن تاحد بیشتری صورت می پذیرد تا کلیه مواد معدنی با ارزش از گانگ همراه آزاد شود .خوراک آسیا از محصول نهایی سنگ شکن تهیه می شود .درداخل آسیای گرذان از گلوله های آهنی ، فولادی ،میله های فولادی یا از خود مواد معدنی برای خردایش استفاده می کنند .این ابزار ها درداخل آسیا عمل نرم کردن را به صورت سایش ، اصطکاک ،ضربه انجام میدهند .
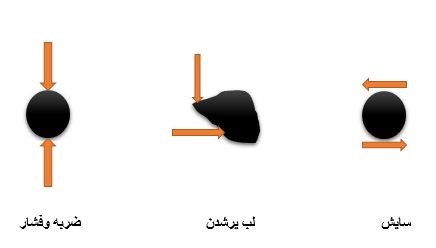
آسیا های گردان
آسیا های گردان به سه نوع اصلی میله ای (rod mill) ، گلوله ای (ball mill) و خودشکن (Autogenousmill) تقسیم بندی میشوند.
هرچه ذرات خوراک بزرگتر باشند قطر آسیا نیز بزرگ میشود و طول آسیا متناسب قطر تغییر میکند.
آسیای میله ای
این نوع آسیا، استوانهای شکل است و بار خردکننده آن را میلههای فولادی تشکیل میدهد که به منظور آسیاکردن اولیه مواد مورد استفاده قرار میگیرد. میلهها به صورت موازی با طول آسیا، درون آن قرار میگیرند و طول آنها حدود ۱۵۰ میلیمتر کوتاهتر از طول داخلی آسیا میباشد. عمل خردکردن در آسیاهای میلهای تقربیا شبیه آسیاهای گلولهای میباشد، اما در این مورد کل طول میله مسئول خردکردن ذرات داخل آسیا است. عمل خردایش در اثر گردش آسیا صورت میگیرد که بخشی در اثر ضربه ناشی از سقوط میلهها بر روی یکدیگر و بخشی در اثر سایش مواد بین میلهها و همچنین بین آنها و جدار داخلی آسیا است. محصول خروجی آسیای میلهای خیلی یکنواختتر از محصول آسیای گلولهای است، اما ابعاد کلی آن درشتتر میباشد؛ بنابراین عموما در انتهای فرآیند خردایش با آسیای میلهای، یک آسیای گلولهای در مدار میباشد (بویژه در جاهایی که محصول ریزدانه نیاز باشد).
بیشتر آسیاهای میلهای مورد استفاده در فرآوری مواد معدنی از نوع آسیاهای تخلیه سرریز میباشند.
آسیاهای تخلیه شبکهای و تخلیه محیطی هم مورد استفاده قرار میگیرند.
حداکثر طول میلههایی که مورد استفاده قرار میگیرند ۶/۶ متر است. طول میلهها حدود ۱۰۰ تا ۱۵۰ میلیمتر کوتاهتر از طول داخلی آسیا میباشد. دادههایی که توسط رولند جمعآوری شد نشان میدهد که نسبت طول به قطر آسیاهای میلهای در محدوده ۱/۲ تا ۲/۳ متغیر میباشد. نسبت طول به قطر در این آسیاها باید بزرگتر از ۱/۲۵ باشد تا از در هم پیچیدن میلهها جلوگیری شود. سطح مقطع میلهها معمولا دایرهای است، اما میلههایی با سطح مقطع چهارگوش و شش گوش هم مورد استفاده قرار گرفته است که هیچ مزیتی از نظر عملکرد نسبت به میلههای گرد ندارند، در حالی که میلههایی با سطح مقطع گرد آسانتر جابجا میشوند. آسترهای محافظ پوسته آسیاهای میلهای ممکن است از جنس فولاد یا لاستیک باشند و همراه با لایه لاستیکی پشت لاینرها (ویا بدون این لایه) به دیواره آسیا پیچ و مهره میشوند. ضخامت لاینرها ۶۵ تا ۷۵ میلیمتر و ارتفاع آنها ۶۰ تا ۹۰ میلیمتر است.
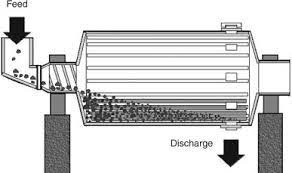
لاینرها دارای طراحیها و نیمرخهای متفاوتی هستند؛ مانند لاینرهای موجی، گوهای یا مستطیلی که به عنوان لیفتر عمل میکنند. لاینرها در قسمت ورودی و خروجی آسیا از فولاد ساخته شده و سطوح صافی دارند. لاینرهای ورودی و سطوح سایشی آنها به توجه به اینکه خوراک آسیا تمایل به تجمع در بخش ورودی دارد، میتواند عمودی و یا دارای شیب باشد. این کار باعث افزایش سایش لاینرهای ورودی و میلهها میگردد که به طور غیریکنواخت فرسایش مییابند. مشاهدات عمومی نشان میدهد که سایش لاینرها در آسیاهای میلهای شدیدتر از آسیاهای گلولهای است.
همچنین برای تعیین اندازه آسیا، باید کار یا انرژی لازم برای نرم کردن کانه تا اندازه مطلوب را تعیین نمود.
آسیای گلوله ای
آسیای گلولهای یا گویآس گونهای از آسیابهای صنعتی است که جهت تولید پودر نرم یا یکنواخت کردن مخلوط به کار میرود. در آسیاب گلولهای از گلولههای فولادی یا سرامیکی برای خرد و نرم کردن مواد غیرفلزی استفاده کنند.
عمده مصارف این نوع آسیاب در تولید رنگ، سرامیک، سیمان و مواد شیمیایی است. در این نوع از آسیاب از تعداد زیادی ساچمه فلزی یا سرامیکی استفاده میشود که با سازوکار همزن یا چرخش دوار آسیاب بهطور دائم بر روی هم حرکت کرده و ذرات درشت را خرد میکنند.
آسیای گلولهای از یک استوانهٔ توخالی که حول محوری افقی یا با زاویهای اندک با افق دوران میکند تشکیل شدهاست. عملیات آسیاب کردن توسط گلولههایی از جنس فولاد (فولاد کروم)، فولاد ضد زنگ، سرامیک یا لاستیک انجام میشود.
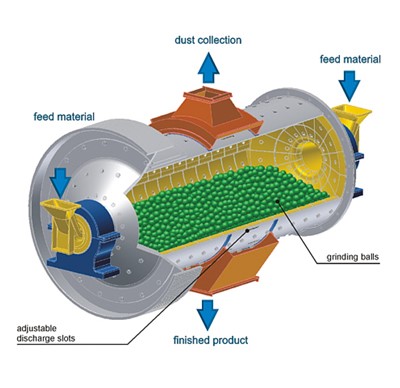
سطح داخلی استوانه معمولاً با مادهای مقاوم در برابر سایش مانند فولاد منگنزیا لاستیک پوشیده میشود. طول آسیاب تقریباً برابر با قطر آن است.
آسیا گلولهای یکی از تجهیزات اصلی مورد نیاز برای آسیاب کردن مواد تکهتکه شدهاست؛ همچنین از آن بهطور گستردهای در خط تولید انواع پودر مانند سیمان، سیلیکات، مواد نسوز، کود، سرامیک شیشهای و غیره استفاده میشود. آسیای گلولهای در صنعت کانه آرایی فلزات آهنی و غیرآهنی نیز کاربرد دارد. آسیا گلولهای میتواند سنگهای معدنی و مواد مختلف را، چه خیس و چه خشک، آسیا کند. مادهٔ آسیابکننده در آسیای گلولهای میتواند متفاوت باشد و بر همین اساس آنها تقسیمبندی میشوند. هر نوع ماده آسیا خواص ویژه و مزایا ی خود را دارا است. خواص کلیدی مادهٔ آسیابکننده عبارت اند از اندازه، چگالی، سختی، ترکیب آن.
اندازه: هر چه اندازهٔ مادهٔ آسیابکننده کوچکتر باشد پودر تولید شده نیز دارای ذرات ریز تری خواهد بود. این نکته قابل توجه است که اندازهٔ گلولهها باید از اندازهٔ ذرات مادهای که قرار است آسیا شود به صورت قابل ملاحظهای بزرگتر باشد.
چگالی: گلولهها باید از مادهٔ ورودی چگال تر باشند. زیرا شناور شدن گلولهها روی مادهٔ ورودی مشکل ساز است.
سختی: مادهٔ آسیا کننده باید به اندازهٔ کافی بادوام باشد تا مادهٔ ورودی را آسیا کند و در همین حال نباید به اندازهای سخت باشد که باعث خوردگی محفظه در سرعتهای بالا شود.
ترکیب: برای کاربردهای مختلف آسیاب، ملزومات خاصی وجود دارد. برخی از این ملزومات بر این اساس تعیین میشوند که مقداری از مادهٔ آسیاکننده در محصول نهایی وجود خواهد داشت. باقی شرایط بر این اساس هستند که مادهٔ آسیاکننده با مادهٔ ورودی واکنش دهد.
گلوله های آسیای گلوله ای
گلولههای فولادی فورج سخت شده برای آسیاهای گلولهای زمانی که سایش شدید و مقاومت شیمیایی مورد نیاز است، بسیار مناسب هستند. همچنین مواقعی که ایجاد حرارت برای فرایندهای آسیاب و پراکندگی تعیینکننده است، میتوان از این گلولهها استفاده کرد. ساچمهها و گلولههای فولادی در آسیابهای سریع و عاری از آلودگی (تر یا خشک) جامدات، پراکندگی مایعات و کاهش اندازه ذرات ریز، همگنسازی فیلرها و موادخام، کاربردهای سایشی و گردسازی در آسیاهای گلولهای، لغزشی، دینو، دانهای، افقی یا عمودی کاربرد فراوانی دارند. فولاد آلیاژی به دلیل دانسیته و سختی نسبی بالای آنها مصارف خاصی در سنگشکنها و مخلوط کردن مواد سخت و سنگین دارند. همچنین در آسیاهایی که فشارها و ضربات شدیدی اعمال میشود یا در فرایندهای مختلف سنگشکنی از این نوع فولادها استفاده میشود. گلولههای فولادی فورج شده نیز مزایای بسیاری را در کاهش اندازه ذرات و پراکنش ریز سیالاتی با گرانروی بالا از خود ارائه میدهند.
بهطور معمول گلولههای فولادی کربنی برای آسیاهای دانهای با سرعت پایین از قبیل آسیاهای فلزات یا پودرهای شیمیایی استفاده میشوند. در فرایندهای آسیاهای گلولهای با سرعت بالا که در ساخت رنگها، جوهرها یا پودرهای رزینی کاربرد دارند، عموماً از گلولههای فولادی آلیاژی کرمدار به دلیل استحکام و مقاومت بالای آنها استفاده میشود.
آسیای خودشکن
آسیای خودشکن برای خردایش خوراک، از واسطه یا بار خردکننده استفاده نمیکند؛ در واقع بار خردکننده آنها قطعات بزرگی از خود بار اولیه است. میتوان از هاردینگ و جکسون به عنوان پدر این نوع آسیاها نام برد. براساس نوشتههای رابینسون چنین آسیاهایی در اواخر دهه ۱۹۵۰ شهرت یافتند. از آن پس آسیاهای خودشکن (AG) و آسیاهای نیمه خودشکن (SAG) بتدریج رشد نموده و جای خود را در مقوله خردایش باز کردند.
آسیاهای نیمهخودشکن، آسیاهایی هستند که در آنها مقداری گلوله فلزی به خوراک اضافه میشود تا در خردایش خوراک، به قطعات درشت سنگ معدنی (بار خردکننده اصلی) کمک کند. مهمترین مزیت آسیاهای خودشکن و نیمه خودشکن عبارتند از: نیاز به سرمایهگذاری اولیه کمتر و قابلیت خردایش مطلوب هر نوع ماده معدنی (شامل خوراکهای چسبنده و رسی).
برخی معتقدند که هزینه بهرهبرداری از این نوع آسیاها بیشتر از سایر روشهای معمول است؛ البته مطالعاتی انجام شده که نشان داده است چنین چیزی ممکن است صحیح نباشد (مطالعات مورل در سال ۱۹۹۱)؛ بنابراین بتدریج مدار آسیاهای گلولهای – میلهای و یا سنگشکنی – آسیای گلولهای، کمتر مورد استفاده قرار گرفتند.
تمام آسیاهای خودشکن و نیمهخودشکن، دارای شبکه فلزی یا لاستیکی در انتهای خود میباشند تا از خروج واسطه خردایش (گلوله فلزی) و سنگهای درشت جلوگیری نماید. این شبکه به پالپ اجازه میدهد که از آن بگذرد و از آسیا خارج شود.
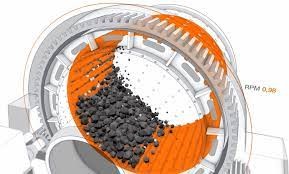
انتخاب نوع آسیا (خودشکن و یا نیمه خودشکن)
انتخاب یک آسیا برای انجام عملیات خردایش خودشکن یا نیمهخودشکن، با در نظر گرفتن این حقیقت که ذرات سخت بزرگ در کانسنگ، خود تشکیل واسطه خردایش (بار خرد کننده) میدهند و از طرفی ابعاد خود این ذرات نیز باید کاهش پیدا کند، پیچیده است؛ بنابراین انتخاب نوع آسیا به عوامل زیر بستگی دارد:
۱) خواص ذاتی کانسنگ
۲) کل توان مورد نیاز توسط آسیا و ترکیب مدار
خواص ذاتی کانسنگ که مهمترین عامل مربوط است و باید محرز شود عبارتند از:
۱) صلاحیت کانسنگ
۲) اندیس کار آسیای نیمهخودشکن (SPI)
کانسنگی مانند کوارتز به راحتی در یک آسیای نیمه خودشکن شکسته نمیشود. کانسنگهای نرم و زودشکن، مانند بوکسیت یا هماتیت، به آسانی شکسته و خرد میشوند. همچنین کانسنگهای رسی و اکسید شده ممکن است بیش از اندازه نرم باشند و نمیتوانند به عنوان واسطه خردایش انجام عمل نمایند؛ بنابراین به عنوان کانسنگهای فاقد صلاحیت یا نامناسب طبقهبندی میشوند (براساس نتایج اسمیت).
گزینه نصب یک آسیای خودشکن و نیمهخودشکن نسبت به آسیای گلولهای زمانی مطرح میشود که مقاومت فشاری کانسنگ، کمتر از ۱۸۰ مگا پاسگال، اندیس کار سنگشکنی باند کمتر از ۲۰ کیلووات ساعت بر تن و اندیس کار آسیای میلهای باند، به طور قابل توجهی بیشتر از اندیس کار آسیای گلولهای باند نبوده، بیشتر از ۱۵ کیلووات ساعت بر تن نباشد.
آستر آسیاها
حفاظ های داخل آسیا کار های مهمی انجام میدهند ، یکی حفاظت بدنه داخلی آسیا در مقابل ضربه و سایش ناشی از گردش بار خرد کننده ، آب و مواد معدنی ، کمک به گردش بار آسیا و جلوگیری از لغزش بار خرد کننده در داخل آسیا ، طراحی مکانیزم خردایش ماننده ضربه ، سایش و فشار بسیاری دیگر، حفاظ ها از قطعات قابل تعویضی ساخته شدهع و در سطح بدنه داخلی آسیا نصب میشوند .
فولاد منگنز دار بهترین آلیاژی است که برای عملیات سخت نسبت به دیگر آلیاژ ها استفاده میشود.
ارتفاع، برآمدگی و مدل حفاظ هامتناسب با نوع عملیات است. معمولا که در آسیا های اولیه (ماننده میله ای ) ارتفاع برآمدگی ها بیشتر از قطر میله در نظر گرفته میشود تا فرسایش و ساییدگی به صورت یکنواخت انجام گیرد. وقتی بار اولیه دانه ریز باشد از پوشش های دندانه دار با زوایای تیز استفاده میشود.
از دیگر حفاظ های و آستر ها میتوان به نوع مستطیلی ، ریلی ، میله ای ، اریب ، کوتاه و بلند ، کوتاه – بلند – متوسط ، لبه قتیقی و پله ای اشاره کرد ، که جهت اهداف خاص در آسیا کردن اولیه و ثانویه به منظور کنترل مکانیزم خردایش و مسیر حرکت بار خردکننده بکار میروند.
چنانچه در حوزه کاری خود به مشکلی برخورد کردهاید و در جستجوی فرد و یا شرکتهای توانمند برای حل مشکلتان هستید می توانید با عضویت در سامانه گلوپ و ثبت مشکل خود با این افراد و شرکت ها ارتباط برقرار کنید.
برای مشاهده مطالب بیشتر به گلوپ پلاس مراجعه فرمایید.
دیدگاه ها
علی اصغر مونسان
ممنون از مقاله خوبتون