صنعت ذوب در کشور ما و در همه جای جهان، ارزش زیادی پیدا کرده و هر روز گسترده تر می شود. کارخانه ی ذوب فولاد اصفهان یکی از قدیمی های صنعت ذوب است. ولی در حال حاضر هزاران کارخانه هستند که بر اساس ذوب کار می کنند و توانسته اند فلزات را با درصد خلوص بالا استخراج کرده و به ورق یا شمش تبدیل کنند که هر کدام این ها می تواند مواد اولیه ای باشد برای صنایع دیگر. اما صنعت ذوب بدون توجه و خرید بگ فیلتر قوی عقیم می ماند.
بنابراین همانقدر که صنعت ذوب گسترش میابد، صنعت کوره سازی نیز پا به پای آن جلو رفته و توانسته خیلی از مشکلات و خلاء های این صنایع را با ساخت کوره های ذوب با مکانیسم های مختلف پر کند.
کوره صنعتی نوعی کوره است که با شکل خاص خود در تکمیل فرآیند ریخته گری مورد استفاده قرار می گیرد. کوره های صنعتی که در صنایع مختلف به کار می روند معمولا ظرفیت بین ۱۵ تا ۲۰ لیتر که ظرفیت بالایی است دارند. کوره هایی که ظرفیت بالاتر از ۱۵ لیتر دارند و دمای کاری آن ها حدودا ۱۵۰۰ درجه است کوره های الکتریکی صنعتی نامیده می شوند.
نحوه کار کوره های ذوب
کوره های ذوب برای گرم کردن بیش از حد مواد جامد تا زمانی که مایع شوند استفاده می شود. اغلب، تجهیزات پردازش حرارتی برای تغییر سطح یا ویژگی های داخلی مواد با افزایش دقیق دمای آنها استفاده می شود. در مورد فلزات، این به طور معمول شکل پذیری را به قیمت سختی و استحکام افزایش می دهد. این به یک کوره صنعتی نیاز دارد که بتواند دماهای کمتر از نقطه ذوب مواد را ایجاد و حفظ کند.
در مقایسه، یک کوره ذوب، دماهای بیش از حد داغی را ایجاد می کند که از نقطه ذوب فلز فراتر می رود و باعث تجزیه ساختار فیزیکی آن می شود که منجر به مایع شدن می شود. این انتقال فاز کاملاً به دما و فشار بستگی دارد. فلزات کمی می توانند در حالت مایع در دمای محیط وجود داشته باشند، به استثنای جیوه (Hg) و یوتکتیک های شناخته شده مانند آلیاژهای مبتنی بر گالیوم (Ga).
برای دستیابی به یک مخلوط مذاب همگن، کوره ذوب باید قادر به تولید و حفظ دماهای لازم در یک دوره زمانی پایدار باشد. چندین معماری کوره ذوب قادر به انجام این فرآیند وجود دارد. در این مقاله، برخی از انواع اولیه کوره های ذوب موجود در بازار را بررسی می کنیم.
انواع کوره های ذوب
رایجترین کورههای ذوب آهن و فولاد که در اکثر کارخانهها مورداستفاده قرار میگیرند شامل کوره بوتهای، کوره کوپلا، کوره القایی و کوره الکتریکی میشوند. هرکدام از این کورهها، تکنولوژی منحصربهفرد خود را دارند که آنها را برای شرایط و ظرفیتهای تولیدی متفاوت مناسب میکند.
علاوه بر کورههای یادشده که برای ذوب فلزات بهمنظور ساخت قطعات استفاده میشوند، کورههای دیگری نیز وجود دارند که برای استخراج فلزات از سنگ معدن آنها به کار برده میشوند. این کورهها شامل کوره رو باز، کوره بسمر، کوره اکسیژن قلیایی و کوره بلند میشوند که اغلب برای آهنسازی و تولید فولاد مورداستفاده قرار میگیرند.
کوره بوته ای
کورههای بوتهای اغلب برای ذوب آلیاژهای غیرآهنی که نقطه ذوب پایینی دارند به کار برده میشوند. مکانیزم این کورهها نیز شامل استفاده از یک پاتیل سرامیکی نسوز است تا در هنگام مواجهه با دمای بالا، بتوانند مقاومت کنند. این پاتیل سرامیکی که بوته نام دارد، در بالای منبع حرارت قرار میگیرد تا فلز و مواد افزودنی موجود در آن ذوب شود. اندازه این بوتهها متفاوت است.
این نوع کوره ذوب دارای ساختار محصور شده است تا حرارت در درون آن نگه داشته شود. سوختهای مصرفی رایج برای کوره بوتهای نیز شامل زغالسنگ یا گاز طبیعی میشوند. در طراحی و سیستم گرمایش کورهها نیز تفاوتهایی وجود دارد. بهغیراز کورههای بوتهای متحرک و ثابت، کورههای بوتهای کج و ثابت نیز وجود دارند. همچنین باید بین کورههای مقاوم در برابر گرمایش و گرمایش با سوخت تفاوت قائل شد.
انواع کوره بوته ای رایج در صنایع ریختهگری عبارتاند از:
- کوره بوتهای ثابت: پاتیل درون این نوع کوره ثابت است و فلز مذاب با استفاده از یک شیر در کف کوره از آن خارج میشود.
- کوره بوتهای متحرک بالابر: زمانی که فلز داخل بوته کاملاً ذوب شد، پاتیل را با کمک جرثقیلهای داخل محل تولید بالا میبرند تا فلز مذاب به قالبها برسد.
- کوره بوتهای کج: پاتیل درون کوره ثابت است و کل سیستم کوره کج میشود تا فلز مذاب از آن خارج شود.
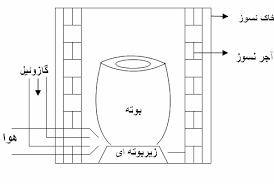
مزایا و معایب کوره بوته ای
از مزایای کوره ذوب بوتهای میتوان به هزینههای سرمایهگذاری پایین و بهرهبرداری و نگهداری ساده آن اشاره کرد. علاوه بر این، امکان ذوب مقادیر کمی فلز و تغییر سریع محتویات بوته نیز وجود دارد. بااینحال، کورههای بوتهای برای ذوب مقادیر زیاد از فلزات و آلیاژها مقرونبهصرفه نیستند، زیرا مصرف انرژی بهشدت افزایش مییابد و عملیات دستی بسیار زمانبر میشود.
کوره ذوب کوپلا
در کوره های کوپلا سوخت و شعله به صورت مستقیم با هم در تماس هستند و نوع سوخت در این نوع کوره، جامد کک و ذغال و گاز مایع (گازوئیل،مازوت،گـــاز طبیعی) است. کوره های کوپلا می توانند به طور مداوم روشن باشند. کوره های کوپلا در سه مدل طراحی شده اند و به سه روش دمش گرم و دمش سرد و با کک می توانند کار کنند.
در نوع دمش گرم کوره به وسیله ی شمش چدن و کک و سنگ آهن شارژ می شود. بعد هوا با دمای معمولی را به داخل کوره می دمند. در این روش سرعت دمش هوا می تواند سرعت ذوب و دما را کنترل کند.
دمش سرد نیز روشی دیگری برای استفاده از سیستم کوپلا است. در این روش برای کاهش میزان کک مصرفی می توانند گازهای خروجی کوره را که دمای بالایی دارند، برای پیش گرم کردن کوره ها استفاده کنند.
در روش آخر که بدون کک است، از سوخت هایی مانند گازوئیل و گاز استفاده می شود این روش آلودگی کمتری دارد.
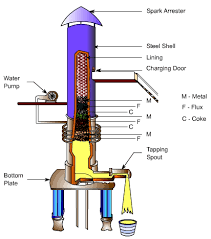
مزایا و معایب کوره کوپلا
این نوع کوره ذوب، ساده و مقرونبهصرفه است و طیف وسیعی از مواد را میتوان با آن ذوب کرد. همچنین، این کوره برای حذف سرباره موجود در آهن کارایی دارد. در مقایسه با کوره الکتریکی، کوره کوپلا مضرات بسیار کمتری دارد. قابلیت ذوب ریزی بالا تا حدود ۱۰۰ تن در ساعت از دیگر مزایای این نوع کوره است. ضمن اینکه به اپراتور چندان ماهری هم نیاز ندارد. مهمترین عیب کوره کوپلا، عدم قابلیت کنترل دما در آن است.
کوره القایی
کورههای القایی از طریق تکنولوژی القای جریان الکترومغناطیسی متناوب، حرارت و دمای لازم برای ذوب فلزات و آلیاژها را تأمین میکنند. این میدان الکترومغناطیسی، سبب ایجاد جنبش در اتمهای فلزات شده که درنهایت منجر به تولید حرارت میشود. منبع جریانهای الکترومغناطیسی، کویل یا سیمپیچهای مسی هستند که در اطراف قطعه قرار میگیرند اما با آن تماس فیزیکی ندارند. این نوع کورهها به دلیل تولید مذاب با کیفیت بالا، نگهداری آسان و بازده انرژی بسیارخوب، یک گزینه ایدئال برای صنایع ذوب و ریختهگری هستند.
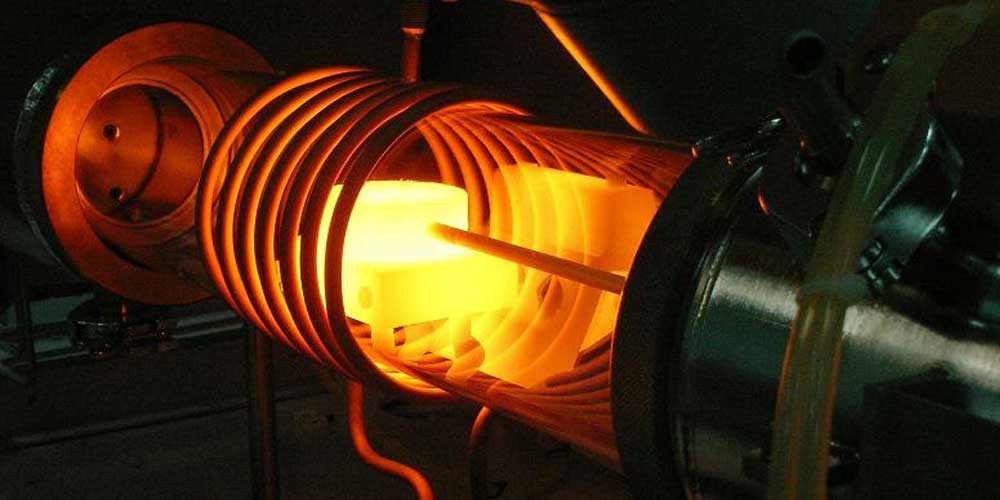
مزایا و معایب کوره القایی
ازآنجاییکه هیچ ارتباط مستقیمی بین فلز و تجهیزات ذوب وجود ندارد، میتوان وضعیت فلز را به روشی بسیار خوب کنترل کرد. بنابراین، از طریق کوره القایی، ترکیبات بسیار دقیق را میتوان با کیفیت بالا به دست آورد. همچنین، انواع فلزات را میتوان در داخل کورههای القایی ذوب کرد مانند چدن، آلیاژهای آهنی و غیرآهنی. ضمن اینکه، قابلیت ذوب در مقادیر کم تا تناژهای بالا از ۱ تا ۱۰۰ تن نیز در این کوره وجود دارد.
از معایب کوره القایی میتوان به این مورد اشاره کرد که سرباره مذاب را نمیتوان با القاء گرم کرد و فقط میتواند توسط فولاد مذاب گرم شود. بنابراین دمای سرباره پایین است که برای واکنش بین فصل مشترک سرباره و فولاد مناسب نیست.
کوره ذوب مقاومت الکتریکی
نوعی از کوره های صنعتی وجود دارد که برای گرم کردن آن جریان برق لازم است. این کوره های صنعتی کوره های مقاومتی نام دارند. این کوره ها برای انجام کار به حرارت نیاز دارند و حرارتشان از نیروی برق تامین می شود. این کوره دارای المنت های گرمایشی است که انرژی برق از درون آنها می گذرد و شرایط مناسبی برای تولید گرما و حرارت را به وجود می آورد. در کوره های مقاومتی امکان تنظیم دما به شکل منظم و دلخواه وجود دارد، به همین خاطر کوره های مقاومتی دقت دمای قابل توجهی دارند.
به دلیل مصرف انرژی بالا توسط کوره های الکتریکی ناگزیر باید هزینه بالایی برای مصرف انرژی پرداخت شود. مورد دیگری که درباره کوره های مقاومتی مطرح است نیاز به زمان طولانی برای ذوب فلزات است به همین دلیل کوره های مقاومتی برای نگهداری مواد مذاب بیشتر مورد استفاده قرار می گیرند. این کوره ها برای ذوب فلزات کمتر مورد توجه هستند.
همان طور که از نام این کوره مشخص است، با جریان الکتریسیته کار می کند اما مستقیم نیست و گرمای آن نتیجه ی مقاومت میله در برابر جریان الکتریکی است. در این مورد شعله و مواد مذاب با هم ارتباط ندارند. با این روش می توان ترکیب شیمیایی موجود در کوره را کنترل کرد. ولی باید بدانید که ظرفیت این کوره ها کم است و حدود ۵۰۰ کیلوگرم می باشد. همچنین به علت استفاده از برق هزینه های انرژی بالا خواهد رفت.
جنس مقاومت ها در این نوع کوره می تواند از نیکل، کروم یا نیکل، کروم، آهن، آلومینیوم باشد.
کوره ذوب قوس الکتریکی
تقریباً یک چهارم تولید جهانی فولاد از یک کوره قوس الکتریکی برای جابجایی الکترود استفاده می کند، که عمدتاً از قوس الکتریکی با ولتاژ بالا برای ذوب ضایعات فولادی برای تبدیل به فولاد مایع بدون تغییر خواص الکتروشیمیایی فلز خاص استفاده می کند.
اکنون سه تا چهار دهه است که کورههای قوس الکتریکی صنعتی برای ساعات طولانیتر، سریعتر و سختتر کار میکنند، زیرا تأسیسات فولادسازی افزایش تولید را در اولویت قرار دادهاند. علاوه بر افزایش تولید و برنامههای عملیاتی فشرده، کورههای قوس الکتریکی بیشتری با الکترودهای بزرگتر، لنجهای اکسیژن بیشتر و در برخی موارد، منابع شیمیایی ثانویه برای تولید توان بیشتر و تقویت رتبه کوره تجهیز شدهاند.
در کوره قوس الکتریکی برای تولید مواد مذاب از الکترود استفاده می شود. الکترود در ناحیه بالایی فلزی که می خواهیم ذوبش کنیم قرار میگیرد و از ناحیه دیگر به خود فلز وصل می شود. وقتی جریان الکتریکی در کوره قوس الکتریکی برقرار می شود در ناحیه اتصال فلز و الکترود دما بالا می رود و اینگونه شرایط مهیای ذوب فلز می شود. به کوره قوس الکتریکی کوره صنعتی جوشکاری نیز می گویند. از این کوره ها در کارخانه ها و صنایع بزرگ استفاده می کنند، چون شرایط مناسبی برای ذوب مواد با سرعت بالا تری فراهم می کند. به دلیل اینکه دمای کوره جوشکاری بسیار بالا است، نمی توان از آن برای ذوب هرگونه فلزی استفاده کرد. برخی از فلزات مانند منیزیم یا آلومینیوم به دمای پایین تری برای ذوب احتیاج دارند. این کوره برای ذوب آلومینیوم منیزیوم مناسب نمی باشد. کوره قوس الکتریکی برای ذوب فلزاتی چون تیتانیوم و فولاد مناسب است چون به دمای بالایی برای ذوب نیاز دارند.
در این نوع کوره، شعله با مواد مذاب در ارتباط است. با دادن جریان الکتریکی بین دوتا الکترود یک قوس الکتریکی ایجاد می شود که قدرت زیادی دارد. الکترودها به داخل کوره می روند و می توانند این جریان را به مواد شارژ شده داخل کوره انتقال دهد. دمای ایجاد شده در آن محدود و تقریباً ۳۰۰۰ درجه می باشد. نکته دیگر درباره قوس الکتریکی استفاده از آهن قراضه برای مواد اولیه است و این امکان وجود دارد که از بدترین آهن قراضه بهترین فولاد را تهیه کنند.
حفظ نکات ایمنی هنگام استفاده از انواع کوره ذوب بسیار پراهمیت می باشد چون با مواد مذاب در هر کدام از کوره های فوق در کمترین حالت چندصد درجه دما دارند که به هیچ عنوان جایی برای سهل انگاری وجود ندارد.
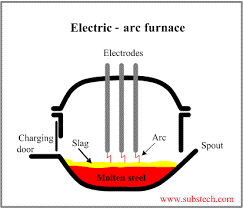
کوره ذوب تشعشعی
کوره های تشعشعی (شعله ای –روباده ) به کوره هائی گفته میشود که بین محصول احتراق و مواد شارژ تماس مستقیم برقرار می باشد و حرارت از سه طریق ، جابجایی ، هدایت و تشعشع به مذاب می رسد. به عبارت دیگر شعله به صورت جریانی از روی سطح شارژ حرکت میکند و در اثر تشعشع شعله، شارژ ذوب میگردد. کورههای تشعشعی (انعکاسی)، معمولاً در دو نوع ثابت و دوار (کوره در حین عملیات ذوب، دوران و چرخش دارد) مورد استفاده قرار میگیرند. کوره تشعشعی ثابت برای ذوب فلزات و آلیاژهای غیر آهنی به کار میرود. کورههای تشعشعی نوع دوار به طور گستردهای برای ذوب چدن، با ظرفیتهای ۳۰۰ کیلوگرم به بالا به کار میرود.
سوخت این کوره ها میتواند مایع، گاز و حتی جامد باشد. ظرفیت این کوره ها بین ۱۵ تا ۷۵ تن متغیر است امّا انواع کوچک آن حتی کمتر از ۵۰۰Kg نیز ساخته شده اند . از این نوع کوره ها به عنوان نگهدارنده نیز استفاده میشود که ظرفیت آنها تا ۹۰ تن نیز میرسد.
مزیتهای کورههای تشعشعی:
- امکان تهیه مذاب با مقادیر زیاد
- برخوردای از راندمان حرارتی بیشتر
- پخش همسان درجه حرارت و ترکیب شیمیایی به دلیل به هم خوردن مذاب
کوره زیمنس – مارتین
حرارت لازم برای ذوب شارژ در کوره زیمنس مارتین توسط گاز و یا سوختهای جامد نظیر ذغال سنگ ویا مایع تامین میشود. سوخت در دو محفظه احتراق که در دوطرف کوره زیمنس مارتین قرار دارند محترق شده و از طریق مشعل هایی به کوره زیمنس مارتین وارد می گردد . دو مشعل قرار گرفته در دو طرف کوره زیمنس مارتین با یکدیگر عمل نکرده بلکه یکی برای حدود ۱۵ تا ۲۰دقیقه کار کرده وسپس با متوقف شدن ان دیگری برای همین مدت کار می نماید واین عمل به تناوب تکرار می گردد .
مواد شارژ کوره زیمنس مارتین :
- آهک
- کلسیم فلورید ( فلوئورین )
- بوکسیت ها
- آجرهای شکسته ی شاموتی
- سنگ آهن
- قراضه فولاد
- چدن خام
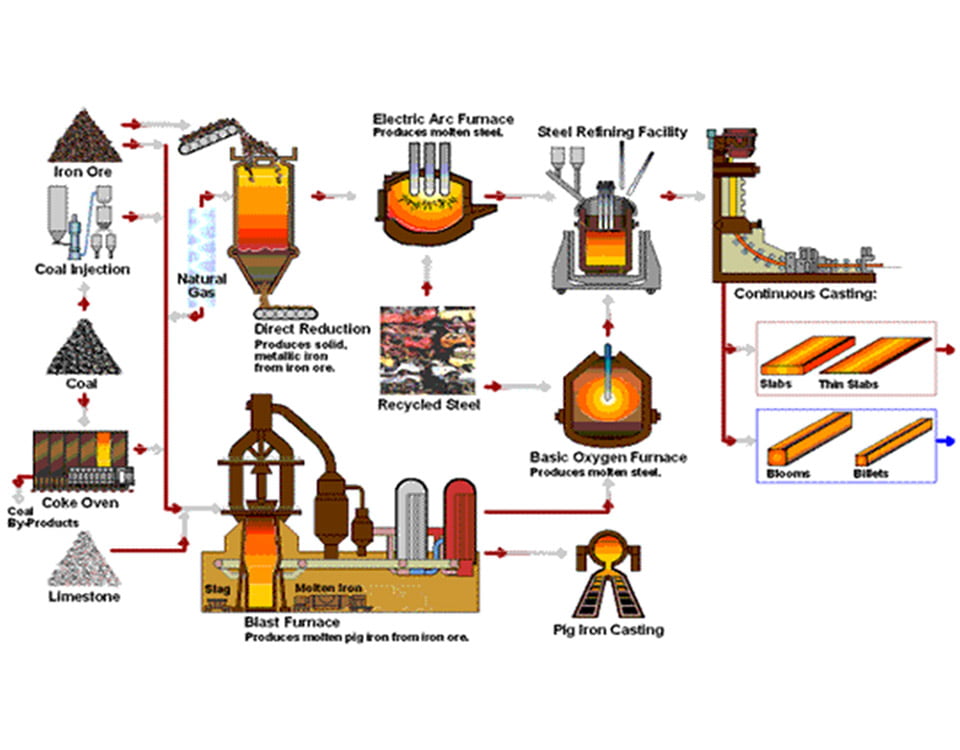
در این مقاله با کوره ذوب و انواع آن آشنا شدیم. برای آشنایی با سایر مطلب در مورد صنعت و معدن مطالب مارا در قسمت مقالات سایت مطالعه نمایید.
چنانچه در حوزه کاری خود به مشکلی برخورد کردهاید و در جستجوی فرد و یا شرکتهای توانمند برای حل مشکلتان هستید می توانید با عضویت در سامانه گلوپ و ثبت مشکل خود با این افراد و شرکت ها ارتباط برقرار کنید.
برای مشاهده مطالب بیشتر به گلوپ پلاس مراجعه فرمایید.