ورق های فولادی جزو پرکاربردترین محصول آهنی در بازار آهن آلات به شمار می روند که خود از شمش فولاد و به روش های خاصی به شکل ورق تولید می شوند. خود ورق های فولادی در همه انواع خود مثل گالوانیزه، استیل یا عرشه فولادی با روشی به نام رول فرمینگ ورق به شکل های دیگری همانند پروفیل، لوله و غیره فرم داده می شوند. رول فرمینگ ورق توسط دستگاه به روش های سرد و گرم می باشد . عملیات رول فرمینگ ورق به دلیل مزایایی که دارد مورد توجه تولیدکنندگان محصولات فولادی قرار گرفته است.
رول فرمینگ ورق فرآیندی است که در طی آن ورق های فولادی نظیر گالوانیزه، ورق های سرد و استیل توسط دستگاه مخصوصی به اشکال مختلفی تبدیل می شوند. محصولاتی که توسط رول فرمینگ ورق تولید می شوند می توانند به هر شکلی که نیاز باشد نظیر انواع پروفیل های فلزی، لوله، ورق طرح دار و غیره شکل داده شوند. به طور کلی رول فرمینگ به روش های تغییر شکل دادن ورق فلزی به واسطه دستگاه رول فرمینگ گفته می شود. در طی این عملیات ورق های فلزی روی شافت های دستگاه که با یاتاقان مهار شده اند جایگذاری می شوند و بعد با توجه به نوع قالب و روش مورد نظر ورق ها به فرم دلخواه تولید می گردند. رول فرمینگ ورق یک روش نوین، بهینه و کاملا انعطاف پذیر می باشد، که تولید هر طرحی روی ورق های فلزی را امکان پذیر کرده است.
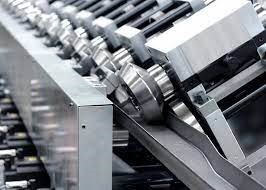
انواع سیستم های رول فرمینگ
مهمترین عضو یک خط رول فرمینگ، دستگاه نورد است. دستگاه نورد نیرو و پشتیبانی لازم را به غلتکها وارد میکند که باعث شکل دهی به فلز میشود.
تنوع در طراحی دستگاههای نورد نامحدود است اما میتوان آنها را در دستههای زیر طبقه بندی کرد:
معلق (cantilevered)، دوپلکس (duplex)، دوپلکس ترکیبی (through-shaft duplex)، استاندارد و صفحهای rafted)).
دستگاههایی که در هیچ یک از دستههای بالا قرار نگیرند را میتوان به عنوان دستگاههای نورد خاص در نظر گرفت.
اجزای اصلی دستگاه نورد
پایه یا بستر:
پایه یا بیس سیستم نورد که گاهی اوقات بستر هم نامیده میشود، دروازهها، شفتها، غلتکها، محرک و سایر اجزای مورد نیاز برای شکل دهی مقاطع را نگه میدارد.
مهمترین الزامات برای این پایه عبارتند از:
- داشتن استحکام لازم در طول عملیات، جابجایی و نصب
- داشتن سطح صاف و هموار برای نصب اجزا
- داشتن یک شیار یا جاخار برای تنظیم کردن دروازهها
- داشتن مجرا برای روان کننده عملیات رول فرمینگ
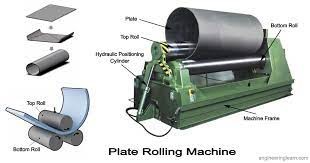
پایههای سیستم نورد بلند ممکن است به دو یا چند بخش تقسیم شوند تا ماشینکاری، جابجایی (بلند کردن) و حمل و نقل آن راحتتر صورت پذیرد.
اگر پایه تقسیم شود یا توسعه آن در صورت نیاز، از قبل پیش بینی شده باشد و یا قرار است بخشهای دیگری بعداً به آن متصل شوند، در این صورت نیاز است که صفحات اضافی و تجهیزات اتصال به انتهای پایه دستگاه نصب شوند.
پایههای دستگاه باید قادر باشد که روانکار مورد استفاده در فرآیند شکل دهی را در خود جای دهد. در مورد پایههای جدا شده، باید توجه داشت که گردش ماده روانکار باید به صورت جداگانه در هر پایه صورت گیرد و یک اتصال آببند نیز بین پایهها ایجاد شود.
در اکثر موارد پایه همچنین سیستم محرک را نیز نگه میدارد. جعبه دندههایی که دروازهها را می رانند، به ندرت بر روی پایه جدا نصب میشوند.
استاندارد خاصی برای طراحی پایههای دستگاه نورد وجود ندارد اما اکثر این بسترها از صفحات ورق یا مقاطع لولهای ساخته میشوند. در شکل ۳ یک نوع پایه ساخته شده از ورق نشان داده شده است. سطح بالای صفحه رویی یا به طور کامل ماشینکاری شده یا فقط در امتداد لبه طولی ماشین کاری شده که در آن جا دروازهها و گیربکسها نصب میشوند.
یک جاخار تنظیم در کل طول صفحه بالایی ایجاد میشود. این شیار (یا اجزا دیگر) باید در بازه ۰.۰۰۱ تا ۰.۰۰۲ اینچ (۰.۰۲۵ تا ۰.۰۵۰ میلی متر) و در تمام طول دستگاه باشد حتی اگر از چند بخش تشکیل شده باشد. سوراخهایی به منظور نصب دروازهها و سایر اجزا، دریل و رزوه میشوند. لبههای فوقانی دیوارههای پایه به صفحه بالایی جوش داده شدهاند و لبههای پایینی به یک چارچوب یا قاب متصلاند. صفحههای مقطع و سایر عضوها به دیوارهٔ پایه جوش داده میشوند که سبب استحکام و صلبیت بیشتر آن میشود.
برای ایجاد یک جریان بازگشتی به روانکار، اغلب این دستگاههای نورد یک کانال در محیط بالایی خود دارند. این کانالها اغلب از نبشیها (structural angle) جوش داده شده به بستر (با فاصله کافی برای روغن و داشتن دسترسی برای تمیزکاری) ساخته میشوند.
بهتر است که پایین کانال به سمت دهانه تخلیه مایع متمایل باشد. در طول ساخت، بالای بال عمودی خارجی نبشی باید بالاتر از بستر دستگاه باشد. این قسمت بالا آمده ماشین کاری و با سطح بستر دستگاه هم سطح میشود تا سبب استحکام بیشتر دروازههای خارجی در طول تغییر یا نصب ابزار شود.
ملزومات اولیه برای ساخت چارچوبهای اسکلتی یا لولهای مشابه صفحات است. اگر بستر دارای صفحه بالایی پیوسته نباشد، میتوان از یک صفحه کالکتور روانساز نازکتر استفاده کرد.
باید برای ساپورتها و اتصالات موتور، دنده و سیستم انتقال قدرت ملاحضات خاصی رعایت شود. اگر صفحه بالایی در اطراف مرکز دستگاه قطع شود تا فضا برای تسمه یا زنجیر درایو (محرک) فراهم شود، در این صورت باید استحکام و صلبیت بستر باید دوباره مورد بررسی قرار گیرد، شاید احتیاج به تقویت قسمت برش خورده باشد.
در دستگاههای نوردی که حرکت جانبی روی ریل دارند، باید پشتیبانی مناسبی از چرخها (یا لغزندهها) صورت گیرد و نیروهای اعمالی در طول حرکت جانبی باید بررسی شوند.
در اغلب موارد، ارتفاع بستر دستگاه برای تأمین خط انتقال مناسب محصول محاسبه میشود. معمولاً ارتفاع خط انتقال در حدود ۳۶ تا ۴۰ اینچ (۹۰۰ تا ۱۰۲۵ میلی متر) از سطح زمین تنظیم میشود. با این حال با در نظر گرفتن اندازه دروازهها، نوع عملیات، عملیاتها ثانویه در طول خط و روش کنترل مواد میتوان ارتفاع دقیق خط انتقال را تعیین کرد.
اگر ارتفاع خط انتقال بیش از حد زیاد باشد، باید یک سکو (walking/working platform) در امتداد قسمت اپراتور دستگاه نورد قرار داده شود. با این حال ایمنی و خستگی (بالا و پایین رفتن مداوم) عواملی هستند که باید در نظر گرفته شوند. از این رو گاهی پرس برش یا تجهیزات دیگر در یک حفره یا گودال نصب میشوند تا یک خط انتقال با ارتفاع مناسب را برای اپراتورها ایجاد کنند.
دروازه نورد
در اغلب موارد، دروازههای سمت درایو در معرض نیروها و گشتاورهای خمشی قابل توجه قرار دارند. دروازههای سمت اپراتور (خارجی) در معرض نیروی کمتری قرار دارند. آنها معمولاً به وسیله یاتاقانهای سوزنی و بوشهای یاتاقان بلند شفتها را نگه میدارند. در نتیجه هیچ نیرویی در جهت محور شفت به دروازه وارد نمیشود.
دروازههای خارجی با یک یا دو پیچ به بستر متصل شدهاند.
نیروهای عمودی شامل پایههای دروازهها میشوند. مقامت در برابر شکل دهی، توقف آنکویلر (uncoiler)، تغییر سرعت غلتکها و گاهی فشردگی نوار نیز باعث ایجاد نیروهای افقی در امتداد حرکت نوار میشوند. این نیروها توسط گشتاور محرک (درایو) تشدید میشوند.
برای تحمل تنشهای حاصل، دروازههای سمت درایو باید محکم و درست به پایه (بستر) تکیه داشته باشند. دروازههای هر دو طرف باید به اندازه کافی محکم باشند تا در مقابل نیروهای جدا کننده شفتها مقاومت کنند. این نیروها گاهی اوقات با نصب یا راه اندازی نادرست یا یک مشکل مثل ضخامت نوار دو یا سه برابر و یا تشدید میشوند.
نیروهای بزرگ، سبب خم شدن شفتها میشوند و انحراف شفت را افزایش میدهند. خم شدن بیش از حد شفت میتواند سطح مقطع محصول را (به ویژه در مورد شفتهای بلند) تغییر دهد. نیروهای شدید میتواند باعث ایجاد تغییر شکل دائمی در شفت شده و در نتیجه محصولات معیوب و ناهمسان خواهند بود.
برای جلوگیری از خرابی و تعمیر هزینهبر شفتهای خم شده، برخی تولیدکنندگان میلههای عرضی (crossbar) با مقاومت محدودی را در بالای دروازهها نصب میکنند. این میلههای عرضی به گونهای طراحی شدهاند که در صورت تشدید بیش از حد نیرو، پیش از تغییر شکل دائمی شفتها، بشکنند. با این حال تعویض آنها نیز زمان گیر است.
یک روش جایگزین استفاده از پیچهای قدرت کالیبره شده برای بستن میلهها عرضی به دروازه است. این پیچها مانند پین برشی عمل میکنند.
بااین حال سادهترین راه برای جلوگیری از انحراف شفت استفاده از یک میله فوقانی الاستیک مانند فنرهای پیش بار شده، یا سیلندرهای هیدرولیکی یا پنوماتیکی است.
در اکثر دستگاههای رول فرمینگ شفتهای پایینی در یک موقعیت ثابت قرار اما شفتهای بالایی میتوانند توسط پیچهای تنظیم بالا یا پایین حرکت کنند. برای تنظیم پذیری دقیق و آسان شفتهای بالایی، پیچهای روی بلوک یاتاقان، و اتصالات آنها به سطح یاتاقان و به میلههای عرضی (cross bar) باید دارای حرکت آزاد باشد (گپ یا شکاف نباید از ۰.۰۰۰۵ اینچ یا ۰.۰۱۵ میلی متر بیشتر شود).
بلوکهای یاتاقان باید به طور آزادانه بالا و پایین حرکت کنند، اما شکاف باید به اندازه کافی کوچک باشد، به خصوص در سمت درایو، تا هنگامی که دروازههای سمت اپراتور (عملگر) برداشته شوند، انتهای شفتها با دست قابل جابجا کردن نباشد.
لازم به تذکر است که هنگام نصب دروازههای سمت درایو، همه شفتها باید دقیقاً با زاویه ۹۰ درجه نسبت به امتداد حرکت نوار نصب شوند. حتی کوچکترین انحراف زاویهای میتواند مشکلات جدی ایجاد کند.
دروازههای سمت درایو معمولاً مجهز به یاتاقانهای مخروطی هستند. این یاتاقانها هم نیروهای عمودی و هم نیروهای محوری را تحمل میکنند. سایش در این یاتاقانها سبب میشود که اتصال آنها با شفت سست شود و در نتیجه نصب دقیق غلتکها امکان پذیر نخواهد بود. بنابراین زمانی که شفتها سست میشوند، لازم است یاتاقانها سفت یا تعویض شوند
زمانی که دروازههای سمت اپراتور برداشته میشوند، گیرههای نگه دارنده در دو انتهای بوشهای یاتاقان، از بیرون افتادن بوشها از بلوک یاتاقان جلوگیری میکنند. هنگامی که دروازهها بر روی دستگاه نصب میشوند، بلوک یاتاقانها باید حدوداً در مرکز بوشها باشد.
انواع قالب فرمینگ
دستگاه رول فرمینگ ورق در قالب های مختلفی وجود دارد. هر دستگاه طرح خاصی را روی ورق های فولادی ایجاد می کند. دستگاه رول فرمینگ نه تنها ورق بلکه نوارهای فولادی را نیز به شکل های مختلف فرم می دهد. لازم به ذکر است که هر طرح ورق که توسط دستگاه رول فرمینگ تولید می شود کاربرد خاصی در صنایع مختلف از جمله ساختمان سازی دارد. انواع قالب های رول فرمینگ را در ادامه بررسی می کنیم.
قالب ورق شیروانی: طرح ورق شیروانی خود دارای چندین طرح مختلف از قبیل کرکره ای، شیروانی شادولاین و شیروانی ذوزنقه ای است. کاربرد این ورق های شیروانی برای سقف ساختمان ها و سوله ها دیده می شود. دستگاه رول فرمینگ ورق شیروانی قابلیت آن را دارد تا ورق های شیروانی در طرح های مختلف تولید کند.
قالب طرح ذوزنقه: این قالب رول فرمینگ ورق به فرمینگ ورق عرشه فولادی نیز معروف می باشد. همانطور که از نامش مشخص است، این ورق فولادی با طرح ذوزنقه نیز برای ساخت سقف انواع سازه ها به کار گرفته می شود.
قالب طرح سفال یا تیپ پالرمو: طرح این قالب بر روی ورق های با ضخامت پنجاه صدم میلیمتر اجرا می شود. فاصله قسمت های خمشی از هم ۲۵ سانتیمتر است و ما بین آنها کمی به سمت بیرون انحنا دارد و صاف نیست.
قالب طرح سفال یا تیپ فرانسه: این طرح که جایگزین سفال برای سقف ها شده است شباهت زیادی به سنگ های سفالی دارد. شکل آن به صورت یک خمیدگی بزرگ دو خمیدگی کوچک و دوباره یک خمیدگی بزرگ است.
قالب طرح پروفیل: این قالب که روی نوارهای ورق فولادی اجرا می شود در طرح ها و شکل های مختلفی مثل پروفیل درب و پنجره، پروفیل گلخانه، پروفیل آلاچیق و غیره تولید می شود. پروفیل های لوله ای نیز به همین شکل قالب زده می شوند.
قالب طرح دیواری یا کانکسی: قالب طرح کانکسی، ورق های فولادی را به شکل چین دار فرم می دهد که چین های داخلی و بیرونی آن باید کاملا یک اندازه باشند. برای ساخت کانکس و کانتینر از این طرح استفاده می شود.
قالب طرح دیواری یا دامپا و نما: این طرح دیواری تقریبا شبیه به طرح کانکسی است با این تفاوت که چین های طرح دامپا و نما مثل طرح کانکسی برابر نیستند. در طرح دامپا بخش های خمیده شده به صورت نیم دایره و در طرح نما بخش های خمشی دارای گوشه هستند.
نحوه فرمینگ ورق های استیل و گالوانیزه
رول فرمینگ ورق استیل
ورق استیل به دلیل فرم پذیری بسیار بالا و همچنین خاصیت ضد زنگ برای فرم دهی توسط دستگاه رول فرمینگ ورق بسیار مناسب است و جزو ورق های محبوب و پرکاربرد به شمار می رود. ورق های استیل در انواع و گریدهای مختلفی در بازار عرضه می شوند ولی مناسب ترین آنها ورق استیل سری ۴۰۰ و به خصوص گرید ۴۳۰ است. ورق استیل گرید ۴۳۰ بیشترین حالت فرم پذیری را دارد و از این جهت برای قرارگیری در دستگاه رول فرمینگ ورق مناسب تر است.
رول فرمینگ ورق گالوانیزه
ورق گالوانیزه یکی از انواع ورق های پرکاربرد در حوزه آهن آلات به شمار می رود. ورق گالوانیزه نوعی ورق است که با پوششی از روی ضد زنگ شده و نیز در انواع رنگ ها تولید می شود. این نوع ورق وقتی توسط دستگاه رول فرمینگ فرم دهی شود برای کاربردهای بسیار زیادی مورد استفاده قرار می گیرد. برای فرم دهی ورق های گالوانیزه از انواع با ضخامت ۱.۸ تا ۶ میلیمتری آن استفاده می شود. اشکال متنوعی را با ورق های گالوانیزه می توان تولید کرد که یک طرح سنتی همان طرح سینوسی است که اغلب برای سقف های کاذب و سقف شیروانی مورد استفاده قرار می گیرد.
یکی دیگر از طرح های مورد استفاده در رول فرمینگ ورق برای ورق های گالوانیزه طرح ذوزنقه است که برای اماکن پرتردد و مرطوب بیشتر مورد استفاده قرار می گیرد. البته خود طرح ذوزنقه در طرح های دیگری همچون دامپا و نما تولید می شود که هر کدام کاربرد به خصوصی دارد. رول فرمینگ ورق گالوانیزه به دلیل تنوع بالا و زیبایی از محبوبیت ویژه ای برخوردار است. ضمن اینکه این ورق ها از مقاومت بالایی برخور دارند و در مقابل فشار ناشی از رول فرمینگ به ندرت پیش می آید تا شکنندگی یا دفرمگی در آنها ایجاد شود.
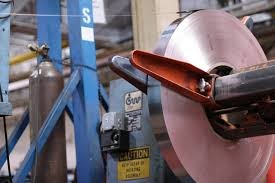
مزایای رول فرمینگ ورق
رول فرمینگ ورق یک روش بسیار مدرن برای فرم دهی انواع ورق های فلزی نظیر آلومینیوم، استیل، گالوانیزه و غیره است. این روش فرم دهی مزایای زیادی نسبت به روش های سنتی از قبیل روش دستی، پرس و خم کاری دارد. در این بخش برخی از مزایای این روش پیشرفته توضیح داده شده اند. یکی از مزایای این روش عدم نیاز به نیروی انسانی زیاد و اپراتور مستقیم است. به این دلیل نیز سرعت کار بالا رفته و در مدت زمان کم مقدار بیشتری از ورق های فلزی فرم دهی می شوند. به عبارت دیگر سرعت رول فرمینگ ورق حدود ده برابر روش های دستی و سنتی است. از دیگر مزایای این روش کم بودن هزینه های تولید است و از نیروی انسانی فقط برای بسته بندی و استقرار محصولات استفاده می شود. مهمترین مزیت این روش این است که محصولات تولید شده دارای یکنواختی و کیفیت بسیار زیاد هستند. معمولا در روش های سنتی طرح های تولید شده ممکن است با انحناهای زیاد و دفرمگی ایجاد شوند و از زیبایی محصول بکاهند که این اتفاق در مورد روش رول فرمینگ به ندرت ممکن است پیش بیاید.
در این مقاله با رول فرمینگ ماشین های نورد وانواع قالب های فرمینگ آشنا شدید. برای مطالعه سایر مقالات مربوط به صنایع فولاد به قسمت مقالات سایت مراجعه کنید.
چنانچه در حوزه کاری خود به مشکلی برخورد کردهاید و در جستجوی فرد و یا شرکتهای توانمند برای حل مشکلتان هستید می توانید با عضویت در سامانه گلوپ و ثبت مشکل خود با این افراد و شرکت ها ارتباط برقرار کنید.
برای مشاهده مطالب بیشتر به گلوپ پلاس مراجعه فرمایید.